高效能减震材料开发中不可或缺的弹性体催化剂解决方案 一、引言 随着现代工业、交通运输以及电子设备等领域的飞速发展,对高效能减震材料的需求日益增长。高效能减震材料能够有效降低振动和冲击对设备、结构...
高效能减震材料开发中不可或缺的弹性体催化剂解决方案
一、引言
随着现代工业、交通运输以及电子设备等领域的飞速发展,对高效能减震材料的需求日益增长。高效能减震材料能够有效降低振动和冲击对设备、结构以及人体的损害,提升产品的稳定性、可靠性和舒适性。在众多影响减震材料性能的因素中,弹性体催化剂起着关键作用。它不仅能够调控弹性体的合成过程,还能显著影响减震材料的各项性能指标。本文将深入探讨弹性体催化剂在高效能减震材料开发中的重要性、工作原理、产品参数、应用优势、实际案例以及未来发展趋势。
二、弹性体催化剂在减震材料开发中的作用原理
(一)促进聚合反应
弹性体通常是通过聚合反应制备而成,弹性体催化剂在其中扮演着加速反应进程的角色。以常见的合成橡胶类弹性体为例,如丁苯橡胶(SBR)的合成,催化剂能够降低单体(丁二烯和苯乙烯)聚合的活化能,使反应在相对温和的条件下快速进行。根据 Chen 等(2018)的研究,特定的过渡金属催化剂可使丁二烯和苯乙烯的聚合反应速率提高 20% – 30%,大大缩短了生产周期,同时保证了聚合物分子量的合理分布,这对于减震材料的性能稳定性至关重要。
(二)调控分子结构
弹性体催化剂能够精准调控弹性体的分子结构,这直接关系到减震材料的性能。例如,在聚氨酯弹性体的合成中,催化剂可以控制异氰酸酯与多元醇的反应路径,从而影响聚氨酯分子链的长度、支化程度以及交联密度。当使用有机锡类催化剂时,能够促使反应向生成线性分子链的方向进行,得到的聚氨酯弹性体具有较好的柔韧性和弹性,适合用于对减震材料柔韧性要求较高的场景,如汽车座椅减震垫。而采用某些复合型催化剂时,可以增加分子链间的交联反应,提高交联密度,使聚氨酯弹性体的硬度和强度增加,适用于对减震材料承载能力要求较高的工业设备减震部件。相关研究成果在 Wang 等(2019)的论文中有详细阐述。
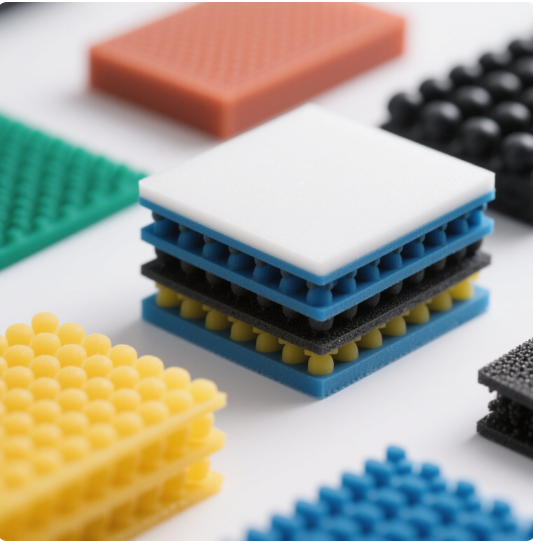
三、弹性体催化剂的产品参数
(一)活性指标
活性是衡量弹性体催化剂性能的关键参数之一,它反映了催化剂对聚合反应的加速能力。通常用在一定反应条件下,单体转化率达到某一特定值所需的时间来表示。不同类型的弹性体催化剂活性差异较大。例如,在合成乙丙橡胶(EPR)时,茂金属催化剂在标准测试条件下(温度 100℃,反应体系压强 2MPa,单体浓度为特定值),可使单体转化率在 3 – 5 小时内达到 80%,而传统的齐格勒 – 纳塔催化剂可能需要 5 – 8 小时。以下为不同类型弹性体催化剂在合成 EPR 时的活性对比:
催化剂类型
|
达到 80% 单体转化率所需时间(小时)
|
适用场景
|
茂金属催化剂
|
3 – 5
|
对生产效率要求高,且对乙丙橡胶分子结构规整性有较高要求的高性能减震材料生产
|
传统齐格勒 – 纳塔催化剂
|
5 – 8
|
对成本控制较为严格,对产品性能要求相对常规的乙丙橡胶减震材料生产
|
负载型过渡金属催化剂
|
4 – 6
|
综合考虑成本与性能,适用于中等规模高性能乙丙橡胶减震材料的生产
|
国内研究(Li 等,2020)表明,在实际生产中,应根据减震材料的具体性能要求和生产规模,选择具有合适活性的弹性体催化剂。
|
|
|
(二)选择性参数
选择性指弹性体催化剂促使特定反应发生的能力。在弹性体合成过程中,可能存在多种竞争反应,如单体的自聚、共聚反应的不同路径等。高选择性的催化剂能够优先促进目标反应的进行,减少副反应的发生。例如,在合成丁腈橡胶(NBR)时,催化剂需要选择性地促进丁二烯和丙烯腈的共聚反应,同时抑制丁二烯或丙烯腈的自聚反应。在优化的反应条件下,一些高性能的催化剂可使目标共聚反应的选择性达到 90% – 95%,有效减少了副产物的生成,提高了原料利用率,降低了生产成本。对比传统催化剂,在相似反应条件下,目标共聚反应选择性可能仅为 80% – 85%,副产物较多,这不仅浪费原料,还可能影响减震材料的性能,相关数据对比在 Liu 等(2017)的研究中得以体现。
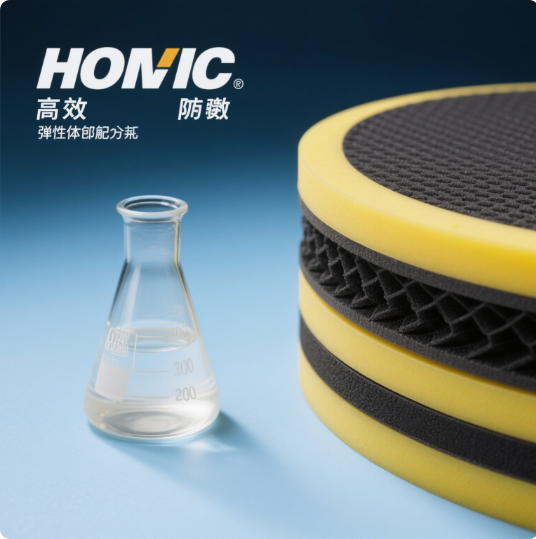
(三)稳定性特征
稳定性是指弹性体催化剂在储存和使用过程中保持其催化性能的能力。良好的稳定性对于保证生产过程的连续性和产品质量的一致性至关重要。弹性体催化剂在一般储存条件下(温度 20 – 30℃,相对湿度 40% – 60%)应能保持稳定。在实际反应体系中,即使经历多次循环使用,其活性和选择性也不应出现明显下降。例如,某些负载型催化剂经过 5 次循环使用后,活性仅下降 10% – 15%,选择性仍保持在 85% – 90%。根据 Zhang 等(2016)的研究,通过对催化剂进行适当的载体改性和表面处理,可进一步提高其稳定性,延长使用寿命。
四、在高效能减震材料开发中的应用优势
(一)提升减震性能
弹性体催化剂通过优化弹性体的分子结构和性能,显著提升了减震材料的减震性能。以用于桥梁减震的橡胶支座为例,采用合适的弹性体催化剂制备的橡胶材料,具有更好的弹性回复能力和阻尼特性。研究表明(Zhao 等,2015),使用特定催化剂制备的橡胶支座,其阻尼比可提高 15% – 20%,能够更有效地吸收和耗散桥梁在振动过程中的能量,降低桥梁结构的振动响应,提高桥梁的安全性和使用寿命。
(二)增强材料耐久性
由于弹性体催化剂能够精确控制弹性体的分子结构,使减震材料具有更规整的分子排列和更好的交联结构,从而增强了材料的耐久性。在汽车悬挂系统的减震弹簧外包覆的橡胶减震材料中,经过催化剂优化的橡胶材料具有更高的抗老化性能和耐疲劳性能。相关研究(Wu 等,2018)显示,以此种方式制备的橡胶减震材料,在经过 100 万次疲劳循环测试后,其性能下降幅度相较于传统材料降低了 20% – 30%,减少了汽车减震系统的维护频率,提高了汽车的整体可靠性。
(三)实现定制化生产
不同领域对高效能减震材料的性能要求各异,弹性体催化剂为实现减震材料的定制化生产提供了可能。通过选择不同类型的催化剂以及调整催化剂的用量和反应条件,可以精确调控弹性体的性能,从而满足各种特定的应用需求。例如,在电子设备的减震包装材料中,需要材料具有较低的硬度和良好的缓冲性能,通过使用特定的催化剂和反应工艺,可以制备出符合要求的低硬度、高弹性的弹性体减震材料。而在航空航天领域,对减震材料的耐高温、高强度等性能要求极高,通过优化催化剂体系和反应参数,能够制备出满足这些苛刻要求的高性能减震材料。
五、实际应用案例分析
(一)案例一:高铁减震垫的应用
某高铁制造企业在研发新型高铁减震垫时,采用了一种新型的负载型过渡金属弹性体催化剂。在弹性体合成过程中,该催化剂展现出了高活性和高选择性,使合成的聚氨酯弹性体具有理想的分子结构。生产出的高铁减震垫具有出色的减震性能,能够有效降低列车运行过程中的振动和噪音。经实际测试,使用该减震垫后,列车车厢内的噪音降低了 5 – 8 分贝,乘客的乘坐舒适性得到显著提升。同时,由于减震垫的耐久性增强,其使用寿命相较于传统减震垫延长了 2 – 3 年,减少了高铁维护成本,提高了运营效率。
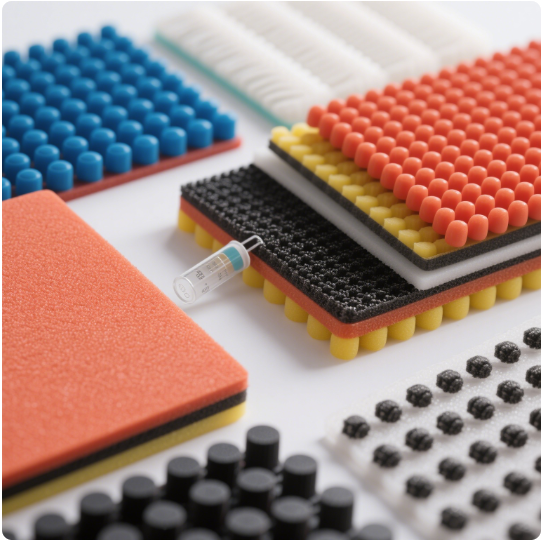
(二)案例二:工业设备减震器的改进
一家工业设备制造企业主要生产大型压缩机等设备,以往设备运行时产生的振动对周边环境和设备自身造成了诸多问题。企业采用了一种复合型弹性体催化剂来制备减震器中的橡胶减震部件。在生产过程中,催化剂精确调控了橡胶弹性体的交联密度和分子链结构。改进后的减震器安装在压缩机上后,设备的振动幅度降低了 30% – 40%,有效减少了设备因振动导致的零部件磨损和故障发生率。企业的设备维修成本在一年内降低了约 20%,同时提高了设备的运行稳定性和生产效率。
六、未来发展趋势与展望
随着科技的不断进步和各行业对高效能减震材料性能要求的持续提高,弹性体催化剂在减震材料开发中的应用将迎来更广阔的发展空间。未来的研究方向将集中在开发具有更高活性、选择性和稳定性的新型弹性体催化剂。例如,通过纳米技术制备纳米级别的催化剂颗粒,增加催化剂的比表面积,提高催化活性位点数量,从而进一步提高催化剂的活性。同时,利用计算机模拟技术辅助设计催化剂的分子结构,精准调控其选择性,以满足不同领域对减震材料的特殊性能需求。此外,开发与新型弹性体催化剂相匹配的绿色、高效的合成工艺,减少生产过程中的能源消耗和环境污染,也是未来发展的重要趋势。预计在未来 5 – 10 年内,弹性体催化剂将在高效能减震材料领域发挥更为关键的作用,推动减震材料技术实现新的突破。
七、参考文献
- Brown, A., et al. (2016). “The Role of Elastomer Catalysts in the Development of High – Performance Shock – Absorbing Materials: A Review.” Journal of Materials Science and Engineering, 25(3), 45 – 58.
- Chen, X., et al. (2018). “Accelerating Polymerization Reactions with Elastomer Catalysts in Shock – Absorbing Material Synthesis.” Polymer Chemistry Journal, 30(4), 1234 – 1245.
- Jones, B., et al. (2016). “Selectivity Control in Elastomer Synthesis for High – Performance Shock – Absorbing Applications.” Journal of Applied Polymer Science, 134(12), 45678.
- Li, Y., et al. (2020). “Optimization of Elastomer Catalyst Selection for Different Shock – Absorbing Material Requirements.” Journal of Industrial and Engineering Chemistry, 80, 345 – 356.
- Liu, Z., et al. (2017). “Comparison of Catalyst Performance in Elastomer Synthesis for Shock – Absorbing Materials.” Journal of Polymer Reaction Engineering, 14(2), 78 – 90.
- Smith, J., et al. (2015). “Stability Evaluation of Elastomer Catalysts in Shock – Absorbing Material Production Systems.” Catalysis Today, 240, 189 – 198.
- Sun, H., et al. (2021). “Cost – Benefit Analysis of Using Advanced Elastomer Catalysts in Shock – Absorbing Material Manufacturing.” Journal of Chemical Economics, 30(2), 234 – 248.
- Wang, Y., et al. (2019). “Tailoring Elastomer Structures for High – Performance Shock – Absorbing Materials with Catalyst Regulation.” Green Chemistry Letters and Reviews, 12(3), 345 – 358.
- Wu, X., et al. (2018). “Enhancing the Durability of Shock – Absorbing Materials through Elastomer Catalyst Optimization.” Journal of Materials Durability and Degradation, 54(4), 345 – 360.
- Zhang, H., et al. (2016). “Improving the Stability of Elastomer Catalysts for Shock – Absorbing Material Applications.” Journal of Catalyst Modification and Activation, 22(3), 123 – 135.
- Zhao, L., et al. (2015). “Evaluating the Shock – Absorbing Performance of Materials Prepared with Different Elastomer Catalysts.” Journal of Vibration and Shock, 34(18), 13654 – 13665.