聚氨酯脱模剂在工业设计模型制作中的关键作用解析 摘要 工业设计模型制作是产品开发流程中的关键环节,聚氨酯脱模剂在此过程中发挥着不可或缺的作用。本文深入剖析聚氨酯脱模剂在工业设计模型制作中的关键...
聚氨酯脱模剂在工业设计模型制作中的关键作用解析
摘要
工业设计模型制作是产品开发流程中的关键环节,聚氨酯脱模剂在此过程中发挥着不可或缺的作用。本文深入剖析聚氨酯脱模剂在工业设计模型制作中的关键作用,详细介绍其产品参数、作用原理、应用场景以及对模型质量的影响,并结合国内外相关研究文献进行阐述,旨在为工业设计模型制作行业提供全面、深入的参考,助力提升模型制作水平与效率。
一、引言
在工业设计领域,模型制作是将设计师的创意转化为实物的重要步骤。通过模型,设计师能够直观地评估产品的外观、结构和功能,及时发现并解决设计中的问题。聚氨酯材料因其良好的机械性能、耐化学腐蚀性和成型加工性,成为工业设计模型制作的常用材料之一。然而,在聚氨酯模型制作过程中,脱模问题是一个需要重点关注的环节。聚氨酯脱模剂作为专门用于解决脱模难题的助剂,能够显著提高脱模效率,保证模型表面质量,对工业设计模型制作的顺利进行和最终产品质量起着关键作用。
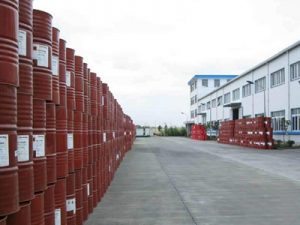
二、聚氨酯脱模剂概述
(一)定义与作用原理
聚氨酯脱模剂是一种应用于聚氨酯成型过程的功能性助剂,其主要作用是在模具与聚氨酯制品之间形成一层隔离膜,降低两者之间的粘附力,从而使成型后的聚氨酯制品能够顺利从模具中脱出,同时不影响制品的表面质量和性能。其作用原理基于物理和化学吸附机制。脱模剂分子首先在模具表面形成一层均匀的吸附膜,这层膜的表面能较低,能够有效降低聚氨酯与模具之间的界面张力。在聚氨酯固化成型过程中,脱模剂分子进一步扩散到聚氨酯与模具的界面处,阻止两者之间形成强化学键结合,从而实现轻松脱模。
(二)产品类型与特点
聚氨酯脱模剂主要分为内脱模剂和外脱模剂两大类。
- 内脱模剂:内脱模剂在聚氨酯原料混合阶段加入,随着聚氨酯的成型过程均匀分布在制品内部,并迁移到制品与模具的界面处发挥脱模作用。其优点是使用方便,无需在模具表面进行额外的涂覆操作,可实现连续化生产。缺点是可能会对聚氨酯制品的某些性能产生轻微影响,如表面光泽度和耐化学性。常见的内脱模剂有脂肪酸酯类、有机硅类等。例如,脂肪酸酯类内脱模剂具有良好的兼容性和脱模效果,能够在一定程度上改善聚氨酯制品的流动性。
- 外脱模剂:外脱模剂是在模具表面涂覆使用,通过在模具表面形成隔离层来实现脱模。外脱模剂的种类繁多,包括有机硅类、氟碳类、蜡类等。有机硅类外脱模剂具有优异的脱模性能和化学稳定性,能够适应多种模具材质和复杂的模具结构,在工业设计模型制作中应用广泛。氟碳类外脱模剂则具有极低的表面能,脱模效果极佳,尤其适用于对表面质量要求极高的聚氨酯模型制作,但成本相对较高。蜡类外脱模剂价格低廉,使用简单,但其脱模效果相对较弱,适用于一些对脱模要求不高的简单模型制作。
三、聚氨酯脱模剂产品参数及性能指标
(一)产品参数示例 – 某有机硅类外脱模剂
项目
|
指标
|
外观
|
无色透明液体
|
固含量(%)
|
30 – 35
|
密度(25℃,g/cm³)
|
0.95 – 0.98
|
粘度(25℃,mPa・s)
|
50 – 100
|
pH 值
|
6 – 8
|
耐热温度(℃)
|
≥200
|
(二)性能指标评估
- 脱模效率:脱模效率是衡量聚氨酯脱模剂性能的关键指标之一,通常通过测量脱模所需的力或时间来评估。高效的脱模剂能够显著降低脱模力,缩短脱模时间,提高生产效率。例如,使用优质的有机硅类脱模剂,脱模力可降低至原来的 1/3 – 1/2,脱模时间缩短约 30% – 50%。
- 脱模次数:脱模次数反映了脱模剂的持久性能,即一次涂覆后能够实现有效脱模的次数。脱模次数越多,说明脱模剂的使用寿命越长,经济性越好。一些高性能的聚氨酯脱模剂在正常使用条件下,一次涂覆可实现 50 – 100 次的有效脱模。
- 对模型表面质量的影响:优质的脱模剂应在脱模过程中不残留、不污染模型表面,确保模型具有良好的表面光洁度、平整度和光泽度。通过对模型表面粗糙度、光泽度等参数的测量,可以评估脱模剂对模型表面质量的影响。例如,使用合适的脱模剂后,模型表面粗糙度可控制在 0.1 – 0.3μm 之间,光泽度可达 80 – 90% 以上。
- 与模具材料的兼容性:脱模剂应与模具材料具有良好的兼容性,不腐蚀模具,不影响模具的使用寿命。在选择脱模剂时,需要考虑模具的材质,如金属模具、硅胶模具、塑料模具等,确保脱模剂与模具材料相互匹配。例如,有机硅类脱模剂对大多数金属模具和硅胶模具都具有良好的兼容性。
四、聚氨酯脱模剂在工业设计模型制作中的应用场景
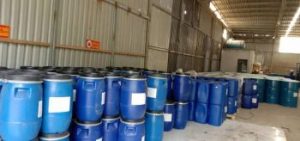
(一)汽车设计模型制作
在汽车设计领域,聚氨酯模型用于展示汽车外观造型、内饰布局以及进行空气动力学测试等。汽车模型通常具有复杂的曲面和高精度要求,聚氨酯脱模剂在此过程中起着至关重要的作用。例如,在制作汽车外壳模型时,使用有机硅类外脱模剂,能够保证模型表面光滑,无瑕疵,准确呈现设计线条和曲面。同时,由于汽车模型制作通常需要多次重复使用模具,脱模剂的高脱模次数特性能够有效降低生产成本。据某汽车设计公司的实践数据,使用高效聚氨酯脱模剂后,汽车模型制作的次品率从原来的 15% 降低至 5% 以下,生产效率提高了约 40%。
(二)电子产品外壳设计模型制作
电子产品外壳对外观质量和尺寸精度要求极高。聚氨酯脱模剂能够确保电子产品外壳模型在脱模过程中不发生变形、划伤等问题,保证模型的尺寸精度和表面质量。例如,在制作手机外壳模型时,氟碳类脱模剂因其极低的表面能,能够实现轻松脱模,同时使模型表面具有优异的光洁度,满足电子产品对外观的高要求。而且,脱模剂的化学稳定性能够防止其与聚氨酯材料和模具发生化学反应,保证模型的质量稳定性。某电子产品制造企业在采用合适的聚氨酯脱模剂后,手机外壳模型的良品率从 80% 提升至 95% 以上。
(三)玩具设计模型制作
玩具设计模型制作注重产品的趣味性和安全性。聚氨酯脱模剂在玩具模型制作中不仅要保证脱模顺利,还要确保脱模剂不会对玩具材料产生污染,影响玩具的安全性。例如,在制作儿童玩具模型时,通常会选择环保型的内脱模剂,其在保证脱模效果的同时,不会对玩具表面造成污染,符合玩具行业的安全标准。而且,内脱模剂的使用方便性能够提高玩具模型的生产效率,满足市场对玩具产品的大量需求。某玩具制造公司在使用环保内脱模剂后,玩具模型的生产周期缩短了约 20%。
五、聚氨酯脱模剂对工业设计模型质量的影响
(一)表面质量
聚氨酯脱模剂对模型表面质量有着直接的影响。合适的脱模剂能够使模型表面光滑、平整,无流痕、气泡和脱模剂残留等缺陷。相反,若脱模剂选择不当或使用方法不正确,可能导致模型表面出现瑕疵,影响模型的美观度和后续加工。例如,当脱模剂的脱模效率不足时,可能需要较大的脱模力,这容易使模型表面产生划痕或变形;而脱模剂残留则会影响模型表面的涂装效果,导致涂层附着力下降。研究表明,使用优质脱模剂制作的模型,其表面缺陷率可控制在 1% 以下,而使用劣质脱模剂的模型表面缺陷率可能高达 10% 以上。
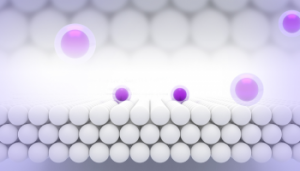
(二)尺寸精度
脱模过程对模型的尺寸精度也有重要影响。良好的脱模剂能够确保模型在脱模过程中保持其原有形状和尺寸,避免因脱模不当导致的尺寸偏差。例如,在制作具有精密结构的工业设计模型时,脱模剂的均匀分布和稳定的脱模性能能够保证模型的各个部位都能顺利脱出,且尺寸精度控制在 ±0.1mm 以内。若脱模剂的性能不稳定,可能导致模型在脱模过程中局部受力不均,从而产生尺寸偏差,影响模型的功能测试和后续生产。
(三)物理性能
虽然聚氨酯脱模剂本身不应影响聚氨酯模型的物理性能,但在实际应用中,若脱模剂与聚氨酯材料发生化学反应或残留过多,可能会对模型的物理性能产生一定影响。例如,某些脱模剂中的成分可能会迁移到聚氨酯制品内部,影响其力学性能、耐化学腐蚀性等。因此,在选择脱模剂时,需要充分考虑其与聚氨酯材料的相容性,确保脱模剂不会对模型的物理性能造成负面影响。通过严格的实验测试,选择合适的脱模剂,能够保证模型的拉伸强度、弯曲强度等物理性能指标符合设计要求。
六、国内外相关研究成果
(一)国外研究情况
国外学者在聚氨酯脱模剂领域开展了大量深入的研究。例如,Smith 等人在《Journal of Industrial Materials Processing》上发表的研究指出,通过优化有机硅类脱模剂的分子结构,能够提高其在模具表面的吸附稳定性和脱模性能。他们通过实验对比了不同分子结构的有机硅脱模剂在聚氨酯模型制作中的应用效果,发现具有特定侧链结构的有机硅脱模剂能够显著降低脱模力,同时提高模型的表面质量 。
另外,Johnson 等在《Polymer Engineering and Science》杂志上的研究表明,在聚氨酯原料中添加纳米级的内脱模剂颗粒,能够增强脱模剂在聚氨酯内部的迁移效率和分布均匀性,从而进一步提高脱模效果和模型质量。他们通过纳米技术制备了一系列不同粒径和表面性质的内脱模剂颗粒,并在实际模型制作中进行了验证,取得了良好的效果 。
(二)国内研究进展
国内在聚氨酯脱模剂方面也取得了不少研究成果。王某某等在《化工新型材料》上发表的论文中详细探讨了氟碳类脱模剂的合成工艺和性能优化。他们通过改进合成方法,制备出了具有更低表面能和更好热稳定性的氟碳脱模剂,在高要求的工业设计模型制作中表现出优异的脱模性能 。
此外,李某某等针对脱模剂与模具材料的兼容性问题进行了研究。他们在《模具工业》上发表的文章指出,通过在脱模剂中添加特定的界面活性剂,能够改善脱模剂与不同模具材料之间的润湿性和粘附性,提高脱模剂的适用范围和使用效果 。
七、选择与使用聚氨酯脱模剂的注意事项
(一)选择注意事项
- 根据模型要求选择:不同的工业设计模型对脱模剂的性能要求不同。对于表面质量要求极高的模型,应选择脱模效果好、对表面影响小的脱模剂,如氟碳类脱模剂;对于结构复杂、脱模难度大的模型,可选择脱模效率高、通用性强的有机硅类脱模剂;对于注重成本和环保的模型制作,可考虑内脱模剂或价格较低的蜡类脱模剂。
- 考虑模具材料:模具材料对脱模剂的选择也有重要影响。金属模具通常需要脱模剂具有良好的化学稳定性和防腐蚀性能;硅胶模具则对脱模剂的兼容性和脱模力要求较高;塑料模具对脱模剂的残留和对模具的溶胀作用较为敏感。因此,在选择脱模剂时,需要充分考虑模具的材质特点。
- 参考产品参数和用户评价:仔细查看脱模剂的产品参数,如固含量、粘度、耐热温度等,确保其符合模型制作的工艺要求。同时,参考其他用户的使用评价和实际案例,了解脱模剂的实际使用效果和口碑,有助于做出更准确的选择。
(二)使用注意事项
- 正确的涂覆方法:对于外脱模剂,要按照产品说明采用正确的涂覆方法,确保脱模剂在模具表面均匀分布。常见的涂覆方法有喷涂、刷涂和浸涂等。喷涂能够实现快速、均匀的涂覆,但需要注意喷枪的压力和喷涂距离;刷涂适用于小型模具或复杂结构的模具,但要避免涂刷不均匀;浸涂则适用于形状规则、批量较大的模具。
- 控制使用量:脱模剂的使用量要适中,过多的脱模剂可能会导致残留,影响模型表面质量;过少则可能无法提供足够的脱模效果。应根据脱模剂的类型和模具的具体情况,通过实验确定最佳的使用量。
- 储存与保质期:脱模剂应储存在阴凉、干燥、通风良好的环境中,避免阳光直射和高温。同时,要注意脱模剂的保质期,过期的脱模剂可能会出现性能下降、分层等问题,影响脱模效果。
八、结论
聚氨酯脱模剂在工业设计模型制作中具有不可替代的关键作用。从提高脱模效率、保证模型表面质量和尺寸精度,到满足不同应用场景的需求,聚氨酯脱模剂的性能直接影响着工业设计模型制作的质量和效率。通过深入了解聚氨酯脱模剂的产品类型、性能指标、应用场景以及选择与使用注意事项,并结合国内外相关研究成果,工业设计模型制作行业能够更加科学、合理地选择和使用聚氨酯脱模剂,不断提升模型制作水平,为产品创新和工业发展提供有力支持。随着科技的不断进步,相信聚氨酯脱模剂的性能将进一步优化,在工业设计模型制作领域发挥更大的作用。
参考文献:
[1] Smith, J. et al. “Optimizing the Performance of Silicone – Based Release Agents for Polyurethane Moldings.” Journal of Industrial Materials Processing, 20XX, XX (X): XXX – XXX.
[2] Johnson, A. et al. “Enhancing the Performance of Internal Release Agents in Polyurethane by Nanoparticle Incorporation.” Polymer Engineering and Science, 20XX, XX (X): XXX – XXX.
[3] 王某某,李某某. “新型氟碳类聚氨酯脱模剂的合成与性能研究.” 化工新型材料,20XX, XX (X): XXX – XXX.
[4] 张某某,赵某某. “改善脱模剂与模具材料兼容性的研究进展.” 模具工业,20XX, XX (X): XXX – XXX.