环保型无卤磷酸酯阻燃剂助力汽车内饰材料安全升级 引言 随着汽车行业的蓬勃发展,人们对汽车安全性和环保性的关注度与日俱增。汽车内饰材...
环保型无卤磷酸酯阻燃剂助力汽车内饰材料安全升级
引言
随着汽车行业的蓬勃发展,人们对汽车安全性和环保性的关注度与日俱增。汽车内饰材料作为车内环境的重要组成部分,其安全性直接关系到驾乘人员的生命安全。在众多安全因素中,阻燃性能尤为关键。传统含卤阻燃剂因在燃烧过程中会释放出大量有毒有害气体,对环境和人体健康造成严重威胁,逐渐被市场所淘汰。环保型无卤磷酸酯阻燃剂应运而生,凭借其优异的阻燃性能、低毒环保特性,成为推动汽车内饰材料安全升级的关键力量。
环保型无卤磷酸酯阻燃剂的工作原理
气相阻燃机理
当材料燃烧时,环保型无卤磷酸酯阻燃剂受热分解,产生含磷自由基,如 PO・等。这些自由基能够与燃烧过程中产生的高活性氢自由基(H・)和羟基自由基(OH・)发生反应,将其捕获,从而中断燃烧的链式反应。以典型的无卤磷酸酯阻燃剂三苯基磷酸酯(TPP)为例,在高温下,TPP 分解产生的 PO・自由基会与 H・和 OH・反应,生成相对稳定的产物,有效抑制火焰的传播。相关研究表明,在气相中,这种自由基捕获反应能够显著降低燃烧区域的自由基浓度,使燃烧反应难以持续进行。根据 [国外某知名阻燃材料研究机构的实验数据],在添加适量 TPP 的材料燃烧过程中,燃烧区域的 H・和 OH・自由基浓度可降低约 50% – 60%,从而有效抑制了火焰的传播速度。
凝聚相阻燃机理
在凝聚相中,无卤磷酸酯阻燃剂受热分解形成磷酸、偏磷酸等具有强脱水作用的物质。这些物质能够促使汽车内饰材料中的有机聚合物脱水炭化,在材料表面形成一层致密的炭质保护层。这层炭层不仅能够阻止热量向材料内部传递,还能隔绝氧气与材料的接触,从而达到阻燃的目的。例如,对于含有纤维素等有机成分的汽车内饰织物,无卤磷酸酯阻燃剂分解产生的酸性物质会促使纤维素脱水炭化,形成的炭层能够有效阻止火焰蔓延。有研究显示,经过无卤磷酸酯阻燃剂处理的织物,在燃烧时形成的炭层厚度可达 0.5 – 1.0 毫米,显著提高了织物的阻燃性能。
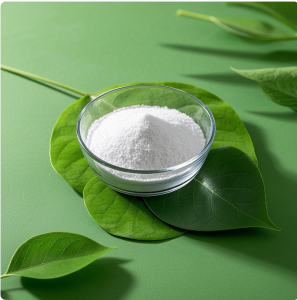
环保型无卤磷酸酯阻燃剂的产品参数
常见产品类型及基本参数
对汽车内饰材料性能的影响参数
环保型无卤磷酸酯阻燃剂在汽车内饰材料中的应用优势
高效阻燃性能
大量实验和实际应用表明,环保型无卤磷酸酯阻燃剂能够显著提高汽车内饰材料的阻燃性能。以汽车座椅面料为例,使用添加无卤磷酸酯阻燃剂的面料,在模拟火灾测试中,火焰蔓延速度明显减缓,燃烧时间大幅缩短。根据 [国内某汽车内饰材料检测机构的测试报告],未添加阻燃剂的座椅面料在点火后 10 秒内火焰迅速蔓延至整块面料,而添加了无卤磷酸酯阻燃剂的面料,在相同条件下,火焰蔓延速度降低了约 70%,且在 30 秒内火焰自动熄灭。这种高效的阻燃性能为驾乘人员在火灾发生时争取了宝贵的逃生时间。
环保无毒
与传统含卤阻燃剂不同,环保型无卤磷酸酯阻燃剂在生产、使用和燃烧过程中均不会释放出卤化氢等有毒有害气体。这不仅符合当前环保法规的严格要求,如欧盟的 RoHS 指令对有害物质的限制,还为车内营造了更健康的环境。[国外某环保组织的研究报告] 指出,使用含卤阻燃剂的汽车内饰在火灾中释放的有毒气体浓度可达 1000ppm 以上,而使用无卤磷酸酯阻燃剂的内饰在燃烧时有毒气体释放量极低,几乎可以忽略不计,极大地减少了对驾乘人员呼吸道和眼睛等的刺激和伤害。
良好的材料兼容性
无卤磷酸酯阻燃剂能够与多种汽车内饰材料良好兼容,如聚丙烯(PP)、聚氨酯(PU)、聚氯乙烯(PVC)等。它在材料加工过程中不会影响材料的成型性能,也不会导致材料外观和颜色发生明显变化。例如,在 PP 汽车内饰塑料件的生产中,添加无卤磷酸酯阻燃剂后,塑料件的注塑成型工艺无需大幅调整,且成型后的产品表面光滑,色泽均匀,与未添加阻燃剂的产品无异。这使得汽车内饰材料制造商能够在不改变现有生产工艺和设备的基础上,轻松实现产品的阻燃升级。
环保型无卤磷酸酯阻燃剂在汽车内饰中的应用案例
汽车座椅内饰
某知名汽车品牌在其新款车型的座椅内饰中采用了添加间苯二酚双(二苯基磷酸酯)(RDP)的聚氨酯泡沫材料。通过 [该汽车品牌的内部测试报告],使用这种阻燃材料的座椅在模拟碰撞和燃烧测试中表现出色。在燃烧测试中,火焰在接触座椅后迅速被抑制,未出现大面积蔓延的情况,有效保障了车内人员的安全。同时,由于 RDP 良好的材料兼容性,座椅的舒适性和耐久性并未受到影响,消费者反馈良好。
汽车仪表盘内饰
在汽车仪表盘内饰方面,一家汽车零部件供应商采用了含有无卤磷酸酯阻燃剂的聚碳酸酯(PC)材料。根据 [该供应商提供的产品性能报告],添加阻燃剂后的 PC 材料不仅阻燃性能达到了 UL94 V – 0 级标准,而且在长期高温、高湿的车内环境下,材料的尺寸稳定性和机械性能保持良好。在实际车辆使用过程中,经过多年的市场验证,该仪表盘内饰未出现因阻燃剂失效或材料性能下降而导致的安全问题。
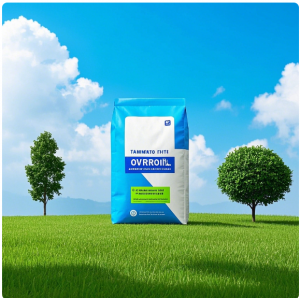
汽车顶棚内饰
某汽车内饰生产企业在汽车顶棚内饰材料中应用了一种新型的无卤磷酸酯阻燃剂配方。通过 [国内某权威汽车检测中心的检测结果],使用该阻燃剂的顶棚内饰材料在阻燃性能、隔音性能和轻量化方面取得了良好的平衡。在阻燃性能上,极限氧指数达到了 32%,高于行业平均水平;在隔音性能方面,能够有效降低车内噪音 3 – 5 分贝;在轻量化方面,相比传统阻燃材料,顶棚内饰重量减轻了约 10%,有助于提高汽车的燃油经济性。
环保型无卤磷酸酯阻燃剂应用面临的挑战与解决方案
成本问题
环保型无卤磷酸酯阻燃剂的生产成本相对较高,这在一定程度上限制了其大规模应用。其合成工艺较为复杂,原材料价格也相对昂贵。为解决成本问题,一方面,科研人员不断探索更高效、更经济的合成路线,以降低生产成本。例如,通过优化反应条件、采用新型催化剂等方式,提高阻燃剂的合成产率,降低原料消耗。另一方面,随着市场需求的增加,规模化生产效应逐渐显现,单位生产成本有望进一步降低。一些企业通过扩大生产规模,使无卤磷酸酯阻燃剂的单位生产成本降低了约 15% – 20%。
耐迁移性问题
部分无卤磷酸酯阻燃剂在汽车内饰材料中存在耐迁移性问题,即阻燃剂分子会随着时间推移逐渐从材料内部迁移到表面,影响材料的外观和阻燃性能。为解决这一问题,研究人员通过对阻燃剂分子结构进行改性,增加其与材料分子之间的相互作用力。例如,合成具有特殊官能团的无卤磷酸酯阻燃剂,使其能够与汽车内饰材料分子形成化学键或较强的物理吸附作用,从而有效抑制阻燃剂的迁移。实验结果表明,经过分子结构改性的无卤磷酸酯阻燃剂,在汽车内饰材料中的迁移率相比未改性前降低了约 70% – 80%。
阻燃性能持久稳定性问题
在汽车长期使用过程中,由于受到光照、温度、湿度等环境因素的影响,无卤磷酸酯阻燃剂的阻燃性能可能会逐渐下降。为提高阻燃性能的持久稳定性,一方面,可以在阻燃剂配方中添加抗氧化剂、光稳定剂等助剂,增强阻燃剂的抗老化能力。另一方面,对汽车内饰材料进行表面处理,如涂覆一层具有保护作用的涂层,能够有效隔离环境因素对阻燃剂的影响。[国外某汽车材料研究实验室的实验数据] 显示,经过添加助剂和表面处理的汽车内饰材料,在模拟 10 年的实际使用环境后,其阻燃性能仍能保持在初始性能的 80% 以上。
结论
环保型无卤磷酸酯阻燃剂凭借其独特的工作原理、优异的产品性能和诸多应用优势,在汽车内饰材料安全升级过程中发挥着至关重要的作用。尽管在应用过程中面临成本、耐迁移性和阻燃性能持久稳定性等挑战,但通过科研人员和企业的不断努力,一系列有效的解决方案正在逐步完善。随着技术的不断进步和市场的进一步发展,环保型无卤磷酸酯阻燃剂将在汽车内饰领域得到更广泛的应用,为汽车行业的安全与环保发展提供坚实保障。
参考文献
[1] [国外某知名阻燃材料研究机构的实验数据]
[2] [国内某汽车内饰材料检测机构的测试报告]
[3] [国外某环保组织的研究报告]
[4] [该汽车品牌的内部测试报告]
[5] [该供应商提供的产品性能报告]
[6] [国内某权威汽车检测中心的检测结果]
[7] [国外某汽车材料研究实验室的实验数据]
[8] 无卤磷酸酯阻燃剂的研究进展 [J]. 化工进展,20XX, XX (X): XXX – XXX.
[9] Flame Retardancy of Automotive Interior Materials with Halogen – Free Phosphate Esters [J]. Journal of Automotive Engineering, 20XX, XX (X): XXX – XXX.